Extracción de la materia prima
Acero Inoxidable
Dado que el hierro no se encuentra en estado puro en la naturaleza, se obtiene principalmente a partir de óxidos y otros minerales.
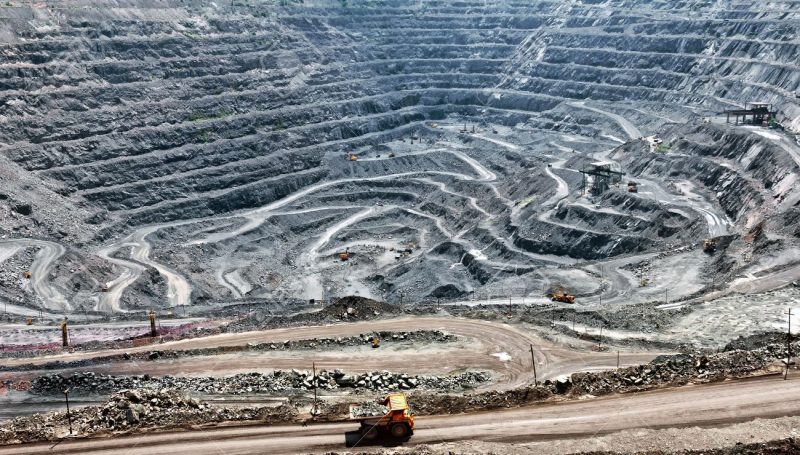
La mayor cantidad de reservas de hierro en minas se encuentran en Australia, en segundo lugar en Brasil, en Rusia y en China. Para extraer el hierro de las minas, en primer lugar se utilizan explosivos para desprender la roca. El material obtenido se transporta en camiones hacia la planta de tratamiento.
Sin embargo, previamente a la llegada a la planta de tratamiento, los camiones pasan por detectores de metales para comprobar que en su carga se encuentre hierro. De no ser así, la carga se desecha. Una vez que la carga llega a la planta, las rocas se trituran.
El material triturado se separa entre aquellos que contienen metal y los que no, a través de uno de dos métodos:
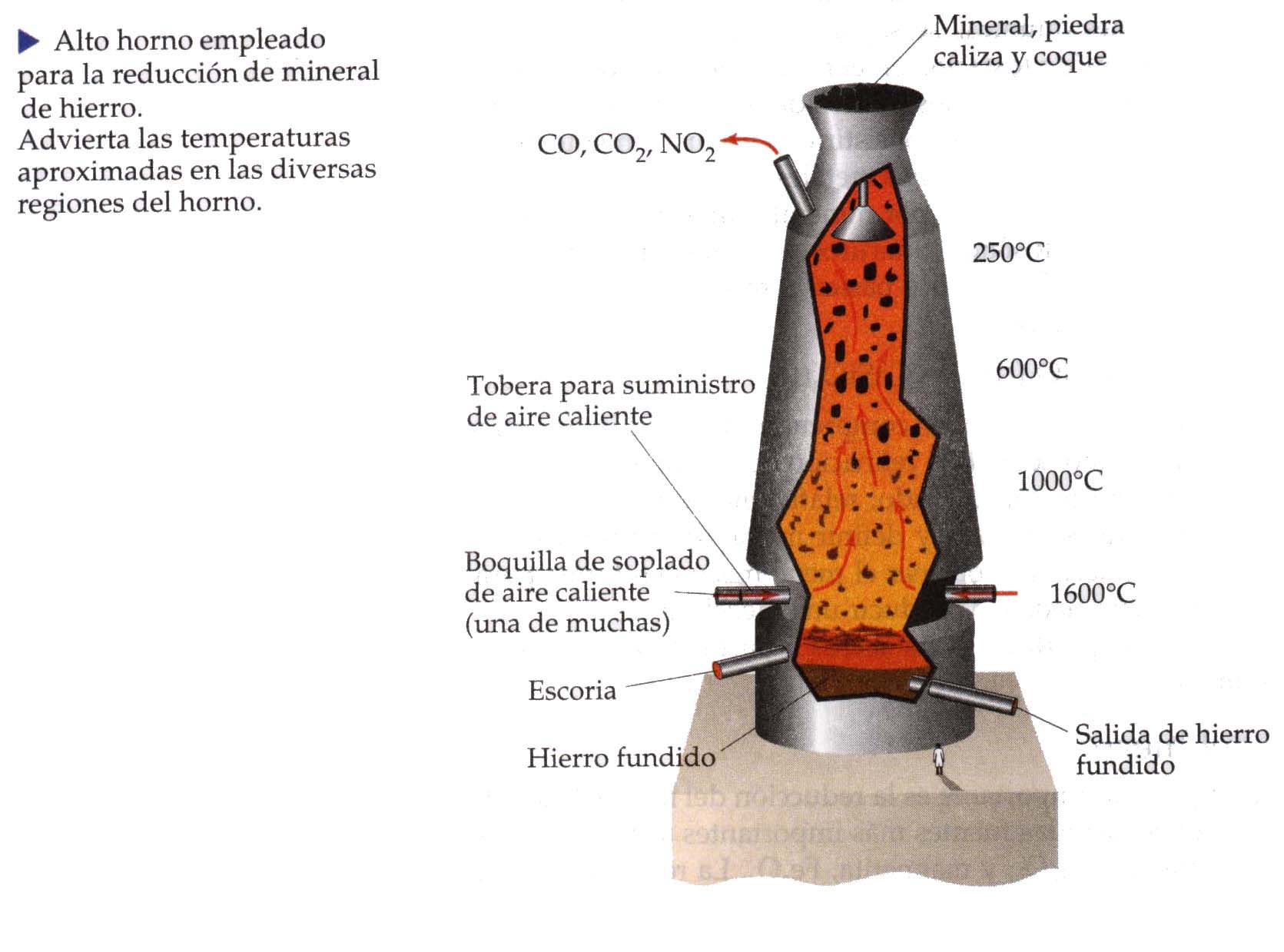
Flotación: Se utilizan detergentes que se adhieren al hierro y lo hacen flotar.
Imanes: Atraen sólo al hierro y no a las rocas.
Los fragmentos seleccionados aún tienen menos del 70 % de hierro.
Para purificarlos, se ubican en un alto horno, donde alcanzan altas temperaturas junto con coque y carbonato de calcio. Al aumentar la temperatura, se forman gases que permiten que el carbono reaccione con el oxígeno, formando dióxido de carbono, y posteriormente monóxido de carbono.
Los óxidos del hierro se unen al monóxido de carbono, formando dióxido de carbono y liberando la molécula de hierro. Una vez que disminuye la temperatura, se elimina el azufre a través de la entrada de aire. De todas sustancias que entraron en el horno, se forman dos fracciones diferenciadas:
Escorias: Mezcla de óxidos y sulfuros.
Arrabio: Sustancia con impurezas pero con alto porcentaje de hierro.
El arrabio luego se somete a nuevas altas temperaturas en hornos convertidores. En estos hornos se inyectan los gases necesarios para producir acero, hierro fundido, hierro forjado, o cualquier otra aleación.
Tomado de: https://www.ejemplos.co/de-donde-se-extrae-el-hierro/
Vidrio
Proceso de extracción
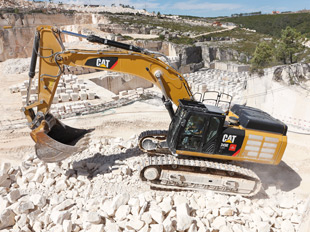
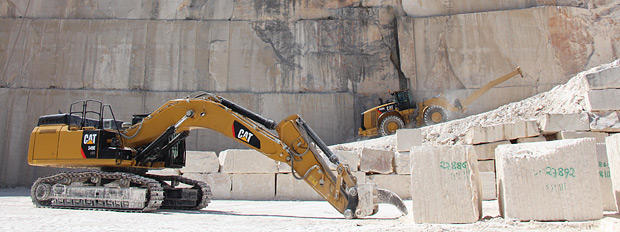
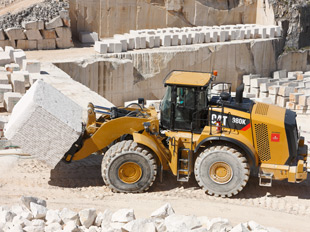
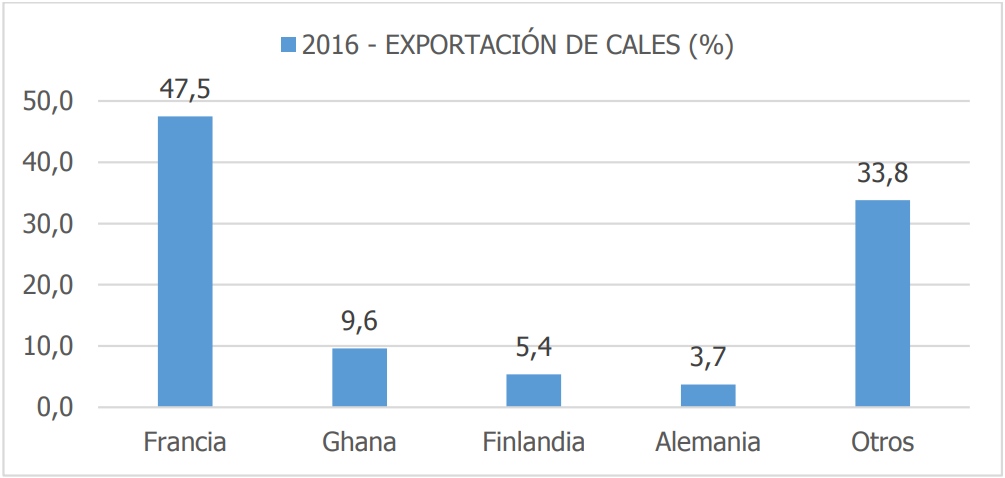
Caliza:
La exploración de la caliza se hace a cielo abierto. Estudiada la existencia de piedra en el local, la extracción pasa por separar la roca de la bancada y dividirla en bloques.
Antes de iniciar la exploración de una cantera, se hace el análisis del recurso. Este estudio averigua la existencia de piedra en el local, su cantidad y la viabilidad económica del proceso. En general, la información sobre las canteras que existen en las proximidades ya es suficiente para seguir con la exploración. No existiendo canteras contiguas, el recurso es analizado recorriendo a un estudio geológico más profundizado.
Si el local tiene las condiciones deseadas para la exploración, el paso siguiente es el licenciamiento de la cantera, procedimiento que comprende varios requisitos ambientales.
Dependiendo de la orientación de la superficie, hay dos formas de iniciar la extracción. Si la superficie es horizontal, se hace una primera cavidad para la inserción del serruche y consecuente corte en la horizontal, permitiendo así la extracción de bloques de piedra más grandes.
Cuando la superficie es vertical o un poco inclinada, la exploración se inicia cortando la roca en la vertical y después por su base. Un trozo de roca queda separado de la bancada (tajada) que puede llegar hasta las 500 toneladas. La tajada es entonces tumbada y, ya en la horizontal, dividida en partes más pequeñas (bloques), en un procedimiento que se denomina tajar el bloque. Las nuevas dimensiones sirven para facilitar el transporte y manejo de la piedra.
Francia es un país que posee grandes reservas de caliza, lo que le ha permitido ganar este mercado y posicionarse como el mayor exportador de caliza a nivel mundial
Arena de sílice:
Se encuentra de forma abundante en grandes playas e incluso áreas desérticas, para su extracción es necesario un cargador frontal para el llenado del camión de transporte que lo llevara a la fabrica donde se fundirá y transformara.
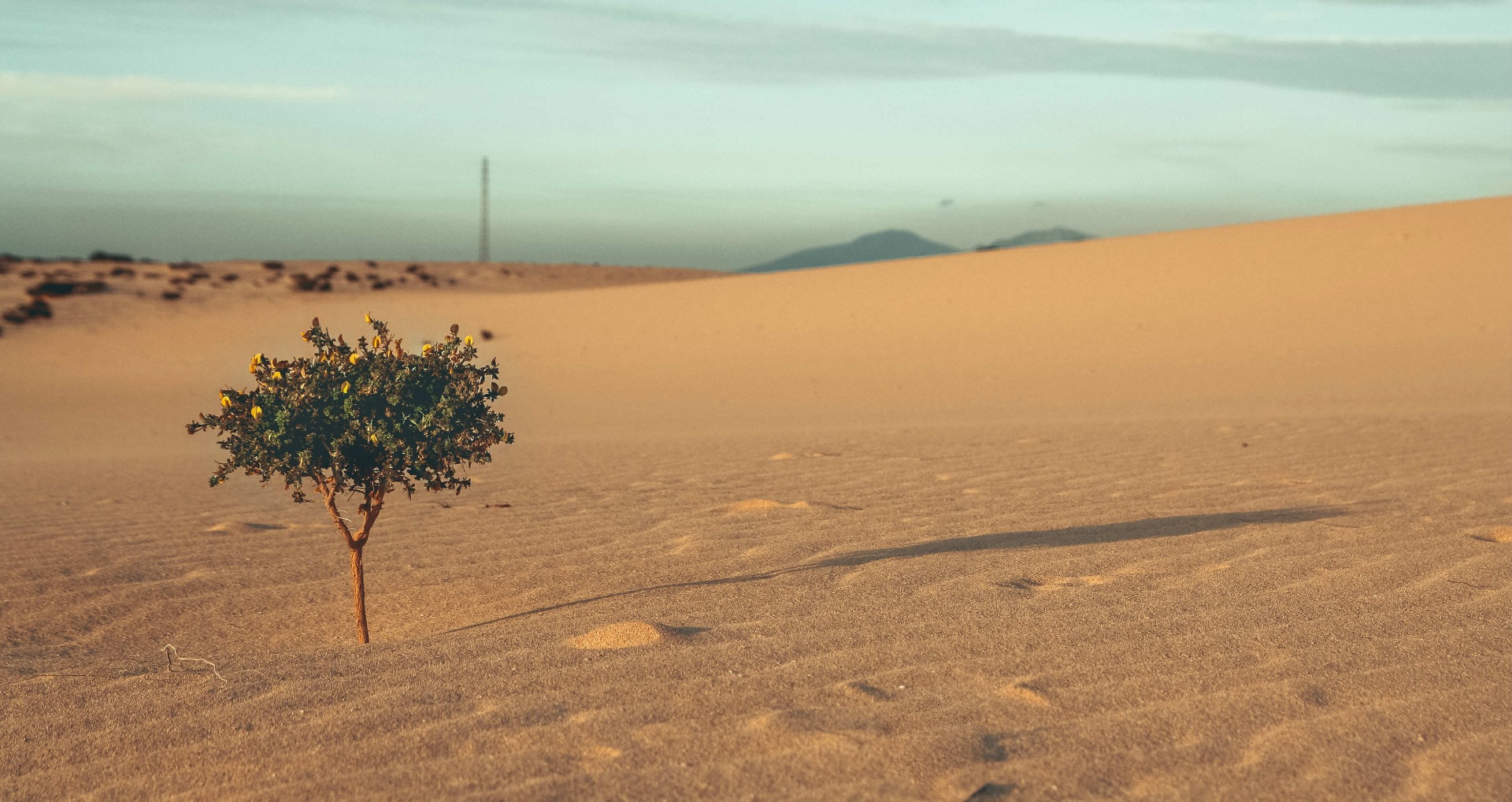
En el siguiente video podemos observar como se realiza este proceso
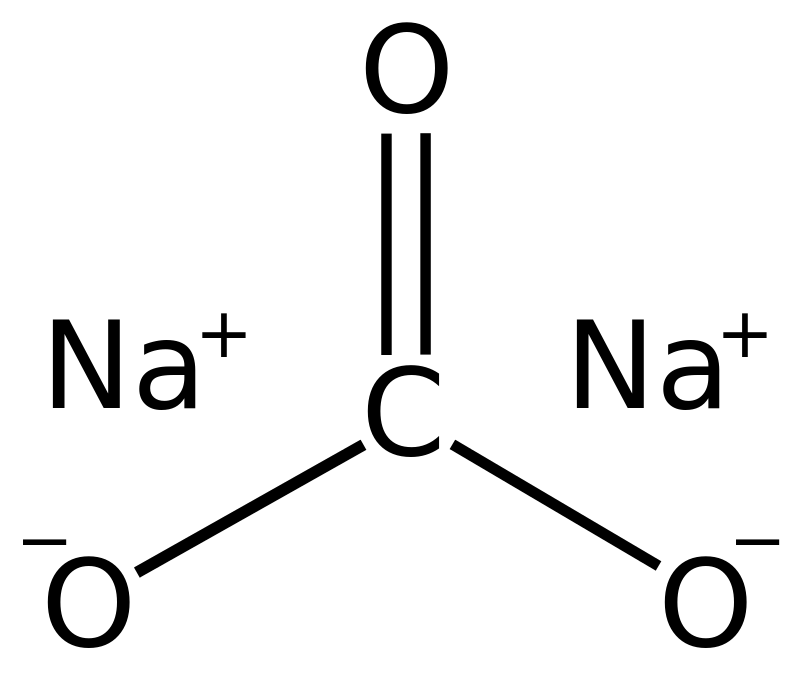
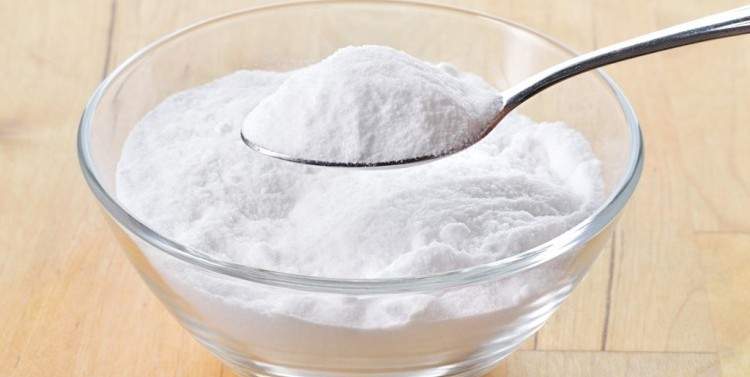
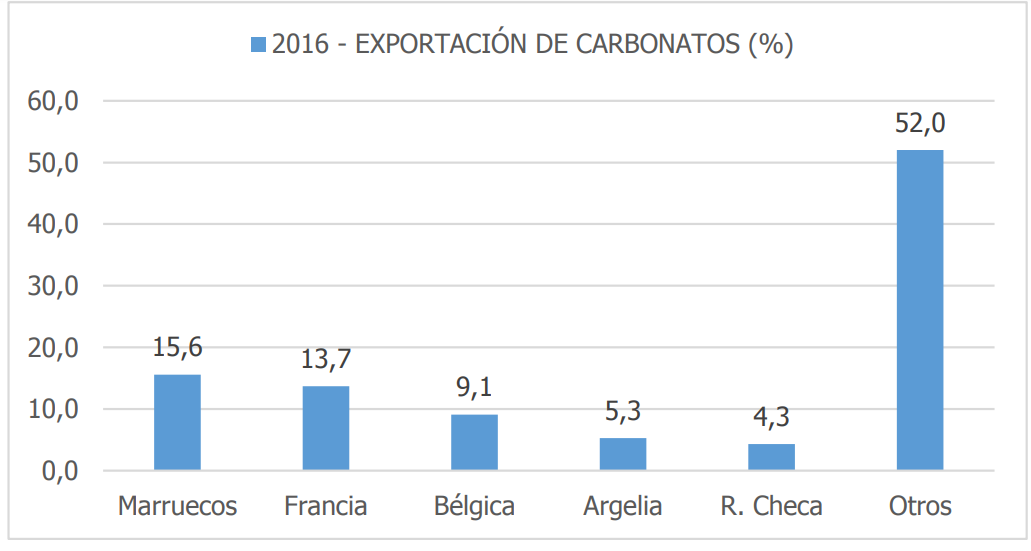
Carbonato de Sodio:
Puede hallarse en la naturaleza u obtenerse artificialmente, gracias a un proceso ideado y patentado en 1791 por el médico y químico francés Nicolás Leblanc. El proceso Leblanc implicaba las siguientes reacciones químicas:
- Reacción de sal común con ácido sulfúrico: 2 NaCl + H2SO4 → Na2SO4 + 2 HCl
- Reacción de calcinación de Na2SO4 con caliza y carbón: Na2SO4 + CaCO3 + 2 C → Na2CO3 + CaS + 2 CO24
Más adelante este método fue sustituido por el método Solvay ideado por el químico belga Ernest Solvay. Solvay fundó en 1863 la compañía Solvay donde utilizó profusamente su método que conseguía abaratar aún más el proceso y eliminar algunos de los problemas que presentaba el método Leblanc. Este método utiliza como materias primas el cloruro de sodio (sal común), el amoníaco y el carbonato de calcio (piedra caliza). En 1915 se cerró la última fábrica de sosa Leblanc
Los países de mayor Producción de carbonato de calcio son Marruecos, Francia y Bélgica, que a su vez se establecen como principales exportadores a nivel mundial.